What challenges does electrification pose to vehicle drive systems? North American Mining spoke to experts at drivetrain specialists, Dana Inc., and mining OEM, Liebherr Mining, to find out.
By Jonathan Rowland

Electrification of mining vehicles is gathering momentum and represents a “significant shift in the industry,” according to Richard Kraemer, Trolley/Battery Sales Support Manager at Liebherr Mining. “Even as diesel-electric trucks with an ICE-alternator combination and electric propulsion system, mining vehicles can run fully electric when operated under trolley, reducing fossil fuel consumption by up to 70%. The traditional ICE can also be completely removed and replaced with a battery pack and necessary auxiliaries that achieve the same power as before.”
Thus far, probably familiar. But let’s step into the shop and take a look under the hood at the changes electrification requires of vehicle drive systems.
“Drive systems for electric vehicles (EVs) are very different from traditional ICE designs,” began Brad Fowler, global segment lead for Mining at Dana Inc. “We see this transformation playing out in three key areas: opportunities for OEM innovation and differentiation; the reassessment of advanced technologies from nice-to-haves into need-to-haves; and changes in mine infrastructure.”
According to Fowler, electrification is providing OEMs “the space to rethink their approaches to machine propulsion and truly innovate.” For example, the diverse range of drive system choices – including e-Hubs, e-Axles, e-Transmissions, and hybrid-electric designs – allow OEMs to select the one that best fits the duty cycle of any given application, whether they are electrifying current solutions or developing a new platform.
Electric drive technologies are also “forcing increased digitalization of the drive system,” Fowler continued. “Highly complex electric-powered propulsion systems depend on advanced vehicle intelligence to optimize performance, productivity, and reliability – especially as autonomous driving, predictive maintenance, and other capabilities are introduced.”
Fowler’s final point of transformation steps us back again to the wider fleet ecosystem. “EVs aren’t drop-in replacements for their ICE-powered predecessors,” the Dana expert noted. “Changes are needed to accommodate recharging and data analysis, among other factors. For example: OEMs are exploring how onsite power generation and distribution need to be integrated into total site solutions for mine operators.”
Liebherr’s Kraemer also picked up this point. “Electrification requires skilled organization and infrastructure to support electric equipment, such as stationary and dynamic charging, as well as adequate power supply at the mine. Operations will go through a holistic change to implement the new technology, so buy-in from the mine site is critical to the success of the new technology.”
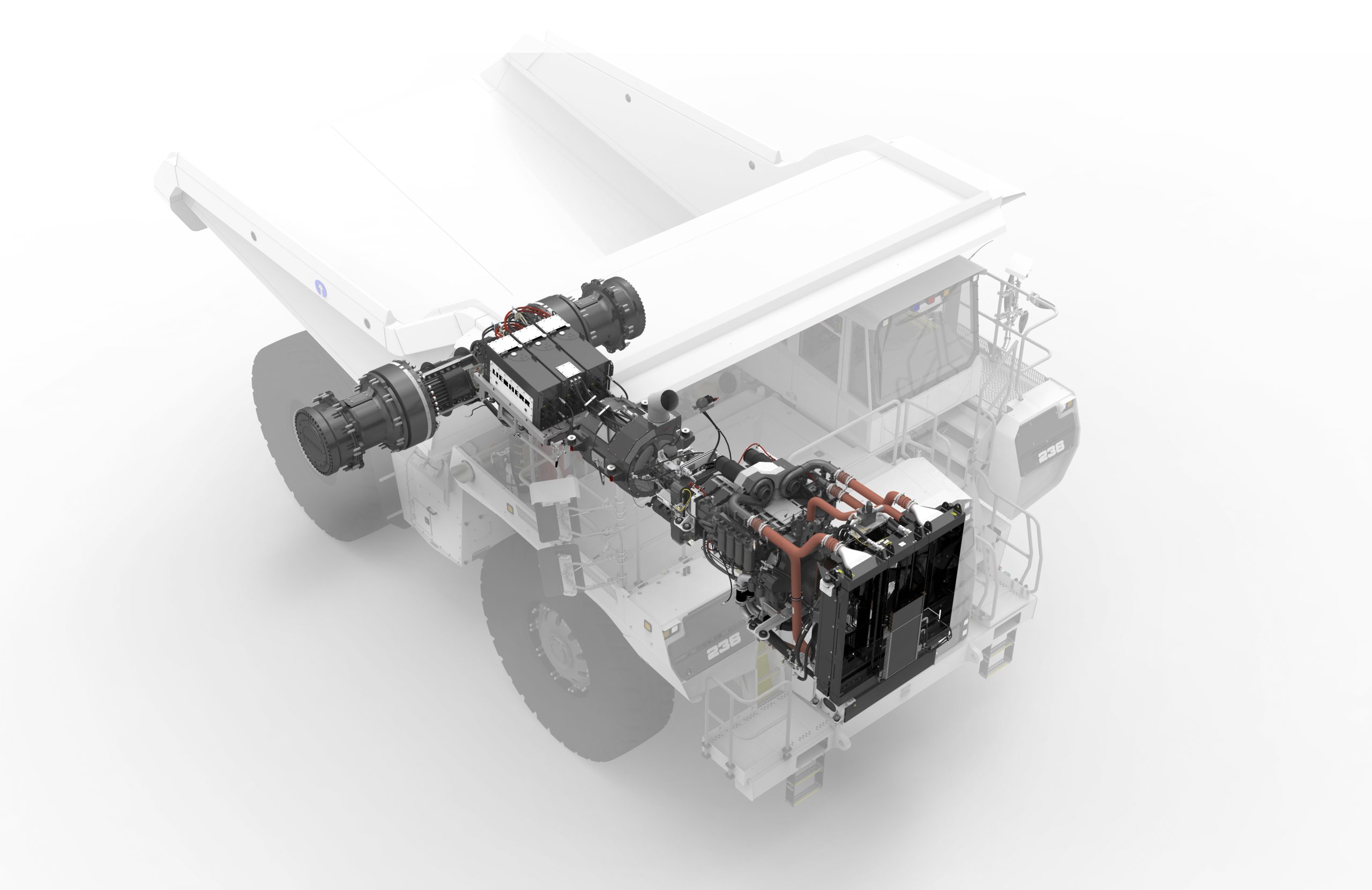
Challenges of electrification for drivetrains and transmissions
Electrification poses “several challenges for drivetrains and transmissions in mining machines,” continued Kraemer. “For example: the new systems must be developed to handle the high torque and power requirements associated with mining operations.”
“The greatest challenge is meeting – and even exceeding – mine operators’ current productivity benchmarks to justify the investment required for electrified equipment,” added Dana’s Brad Fowler. “To accomplish this, it’s important to evaluate the performance expectations of each vehicle, and then design a drive system that delivers. This assessment needs to account for numerous factors, including power needs, duty cycles, package size, weight, operating environments, run time, recharging strategies, maintenance, and owning and operating costs, to name a few.”
For some mining vehicle OEMs this is an easier prospect than for others. Liebherr has offered an electric-drive excavator for more than four decades; the company also utilized diesel-electric drive mining trucks and hydrostatic drive dozers long before the current push to electrify, so “the transition has been easier for us than for mechanical drive machines,” said Kraemer.
Others are finding the complexity challenging to navigate, according to Fowler. “We’re finding some OEMs are increasingly leaning on our expertise across a number of development disciplines to support them in the energy transition. As a result, we’ve transformed into an active co-developer with many of our OEM customers by offering capabilities that include vehicle dynamics, mechanics and mechatronics, electronics, hydraulics, and software and controls.”
A final challenge is the mine environment itself. “The requirements for drive systems operating in harsh and severe environments are significantly higher, and traditional electrification components developed for applications in other markets don’t meet them,” Fowler said. “Reliability, durability, and maintainability are supremely important, especially at remote mine sites where service and maintenance capabilities are often limited.”
Current solutions: flexibility is key
Turning the discussion to current and future solutions, both Fowler and Liebherr’s Kraemer emphasized the importance of flexible solutions that can be tailored to an individual mine’s operating conditions and business needs. This flexibility is at the heart of Dana’s most recent e-Transmission development, the Spicer Electrified eSP502, and of Liebherr’s aim to offer a complete zero-emission mining solution.
Dana’s Spicer Electrified eSP502 e-Transmission
Dana has been a “top-tier supplier to manufacturers of mining equipment for more than 60 years,” said Fowler. “We offer a combination of advanced drive systems, engineering expertise, industry knowledge, global reach, and cross-pollination from Dana’s light- and commercial-vehicle divisions.”
The company’s drive solutions range from hybrid-electric transmissions – which can help OEMs transition smoothly from ICE powertrain designs – to fully electrified e-Transmissions, e-Axles, and e-Hub drives. The company’s latest development is its Spicer Electrified eSP502 e-Transmission, which offers a flexible platform, designed to support the electrification of load haul dumpers and other applications across off-highway markets.
Launched at bauma in 2022, the eSP502 comprises a “dual-motor, two-speed design on a flexible platform that enables optimized performance at maximum efficiency in a compact package,” Fowler explained. “The modular approach to transmission design also allows for a single motor solution, as well as an optional power offtake, depending on the specific vehicle requirements.”
Powered by Dana TM4 electric motors and inverters, the dual-motor version supports continuous power outputs up to 270 horsepower (200 kilowatts), while the single-motor configuration is engineered for 187 hp (140 kW) of continuous output. It also comes with “next-generation control software and functional safety readiness, enabling easy installation and smooth integration for the OEM, and it features optimized power transmission elements that minimize drag and maximize efficiency,” added the Dana expert.
A focus on flexibility continued as Fowler looked to the future. There is “no one-size-fits-all solution for electrification in mining,” he said. “We expect drive solutions will be developed, brought to market, and adopted by customers at different rates. To facilitate this transition, we’re continuously evaluating how we can support OEMs through continued innovation, while helping the make better business cases for equipment buyers.”
The Liebherr zero-emission
mining solution
Customer needs lie “at the center of Liebherr’s product design,” said Kraemer. “Due to the characteristics of the mine, the haul profiles of mining machines and the available charging infrastructure will continue to be specific and unique for each mining application. Our mining machines are thus designed to be both modular and energy-type agnostic. Our battery EVs are also battery chemistry agnostic, allowing us to easily integrate the latest battery technologies into our equipment. Alternative battery chemistries are continually challenged, tested, and offered to reduce cost per tonne.”
Combined with Liebherr’s in-house core competencies and vertical integration of its mining products, this approach enables the company to “identify and realize the best solutions for open-pit mining machines with the right solution for every customer. Our ultimate goal is to provide a Liebherr zero-emission mining solution, thereby simplifying the transition process for our customers, while facilitating their progress to zero emission mining.”
The company has now achieved its target of offering low-carbon solutions for its full range of trucks and excavators through electrification of the drive systems. Its next objective is to “offer fossil fuel-free solutions by 2030, allowing mines to achieve zero emissions with a focus on well to wheel,” said Kraemer.
Liebherr is “on the way” to achieving this goal, thanks to a combination of technological advances, improved efficiency and durability, optimized performance, and a focus on sustainable, efficient, and cost-effective mining operations. “We’re working to provide the necessary ecosystem in combination with battery-powered mining machines and the necessary dynamic and stationing charging solutions. We’re also working on solutions for customers who do not have access to sustainable electricity and therefore developing in-house alternative fuel drives based on combustion engines.”
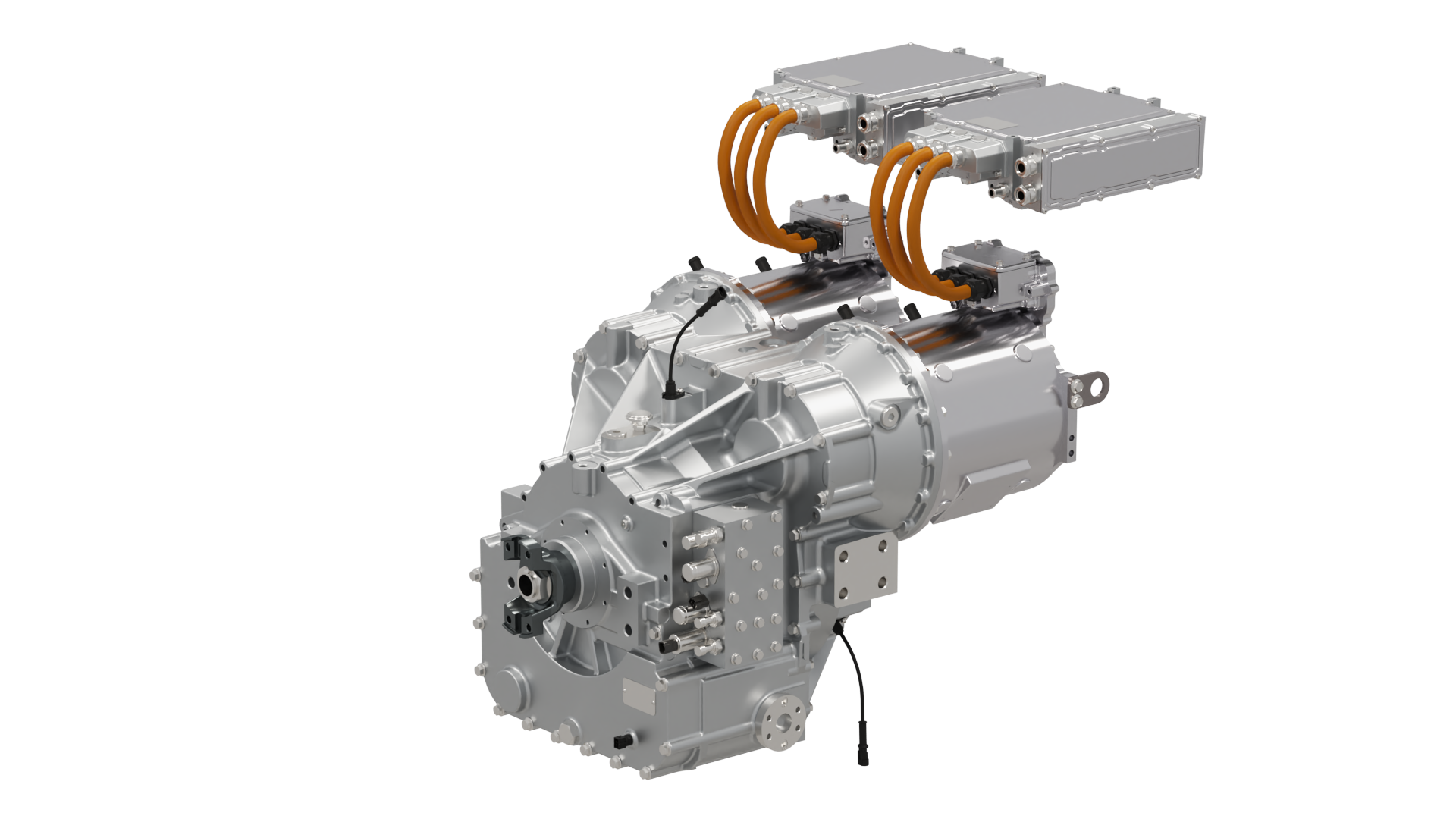
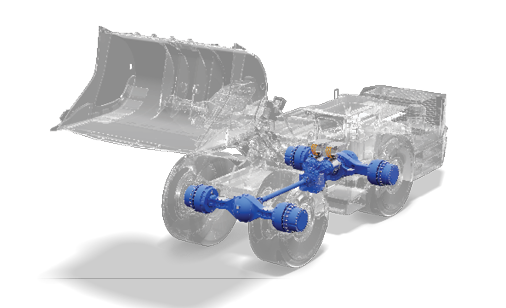
Jargon busting
e-Transmission: Transmissions with directly integrated electric motors. e-Transmissions centrally distribute motive power to the axles through traditional driveshafts. They minimize the impact on vehicle layout when electrifying by maintaining existing axle and driveshaft layouts, and can distribute the 100% of the tractive power to both axles, depending on ground conditions.
e-Hub: Independent wheel final drives with integrated electric motors. e-Hubs place tractive power directly at the wheels, maximizing mechanical efficiency but drastically increasing control system complexity to manage energy distribution to each wheel.
e-Axle: Axles with electric motors, typically integrated into the differential housing. e-Axles distribute tractive power to the front and rear of the vehicle, allowing increased control of traction, with an intermediate increase in control complexity.